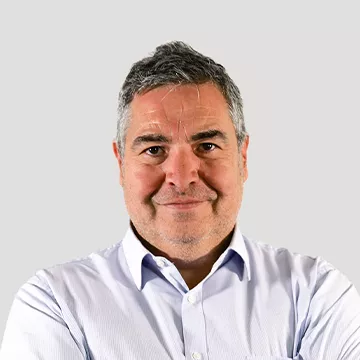
“We are committed to continuous innovation to ensure that we can feed the world sustainably, responsibly and efficiently through technology.”
José María Rubio
Global Manufacturing Industry Lead
#WE ARE
DIFFERENT
#WE ARE
DIFFERENT
We optimize the performance of production processes by integrating efficiency control: OEE (Overall Equipment Effectiveness), energy consumption, and human resource management. With full traceability and accurate mass balances, we provide a clear view of the entire production process.
Real-time monitoring of crop status and environmental conditions enables efficient resource use, such as water and fertilizers. With IoT and predictive analytics, we anticipate risks, improve productivity, and ensure quality, promoting more sustainable agricultural practices.
In a production environment, even the smallest error can quickly multiply and affect a large number of products. Continuous and automated quality control ensures early detection of faults, guaranteeing products that meet the highest standards.
Effective inventory management of raw materials and semi-finished products is essential to avoid both overstock and stockouts. An automated and optimized system ensures a continuous flow of materials without overloading storage resources.
Unexpected breakdowns can halt production, resulting in significant losses. With a data-driven predictive maintenance plan and real-time condition monitoring, we can foresee and prevent failures, minimizing disruptions and optimizing equipment lifespan.
Accurate demand planning is crucial for aligning production with market needs. Data-driven forecasts prevent overproduction or inventory shortages, ensuring an agile response to demand fluctuations.
The automated integration of orders and delivery notes with the ERP system, along with an efficient picking process, guarantees a high fulfillment rate, improving customer satisfaction and reducing logistical errors.
Track a product throughout all its stages, from origin to final consumer. We ensure food safety and quality while providing transparency about production processes.
We manage your production plants visually in real time to enhance production efficiency, processes, and product quality.
Osiris offers functionalities for traceability, warehouse management, labeling, palletizing, logistics, pallet management, analytical dashboards, cost and margin charts and ERP integration.
Strategic alliances with the leading technology providers in the market
Driving the success of leading international companies
#
THINGS
HAPPEN
HERE
“We are committed to continuous innovation to ensure that we can feed the world sustainably, responsibly and efficiently through technology.”
José María Rubio
Global Manufacturing Industry Lead